Design & build of a adhesive dispensing system
Abstract
A production process required an adhesive to be dispensed onto a large assembly to seal electronics against water ingress. Vendors quoted $30-70k and 20-30 week lead times for a system large enough to do the job. To meet project deadlines, a system was developed in-house in 5 weeks for $5000 that exceeded the production needs and meets the process specifications.
A CNC powered fluid dispensing system
During the design and development of a electronically steered array, a large flat panel needed to be sealed against outdoor conditions. This called for mechanically attaching the panel to a rectangular bezel mechanically with screws and sealing the seam between the components with adhesive to ensure the joint meets IP67 ratings. The assembly is relatively large, 16″ x 24″, and called for an automation solution to ensure the seal is repeatable and meets the the daily production throughput of > 100 units per day.
Meetings with automation vendors to get a quote on a system capable of doing this work came in a price tag of $30,000 – $70,000 and a lead times of 20-30 weeks to deliver a working system. Waiting 20-30 weeks for delivery would severely delay the release of the product and adversely impact the revenue goals for the year. Without an automation solution, the labor cost to manually do this work would go up substantially and the seal’s consistency would likely vary by a significant amount.
To meet the automation need inside the available schedule, an automation solution was developed and delivered in-house. A dispensing system from Nordson was identified that could be automatically triggered to dispense a consistent amount of a liquid product. This improves upon part of the consistency problem but still requires an XY motion system to fully ensure repeatability & quality.
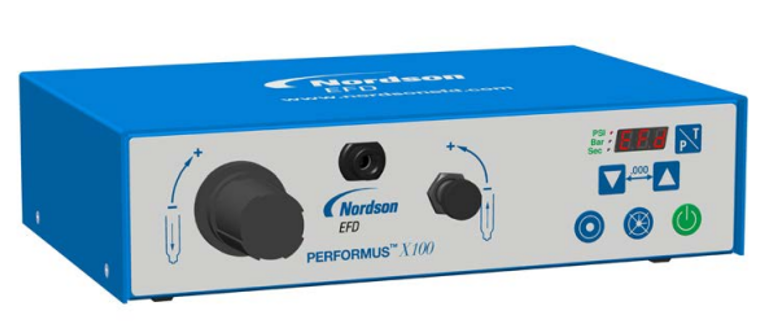
Due to the large size of the assembly to have adhesive dispensed, 16″ x 24″ x 1″, it requires a large motion system to handle the part. The Shapeoko 4 CNC system by Carbide 3D is a familiar CNC router system that has up to 32″ x 32″ x 4″ of working volume at an attractive price of just $2400.
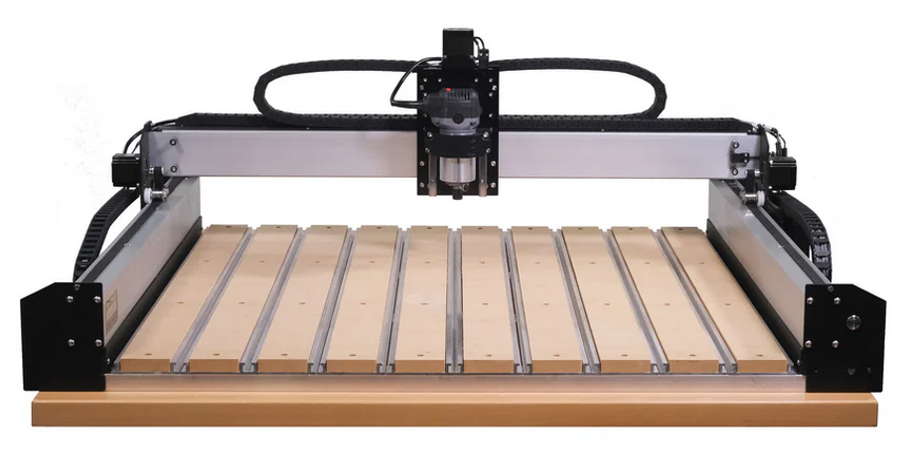
The combination of this CNC platform coupled with the Nordson dispensing system creates the base of a system that can meet the project needs.
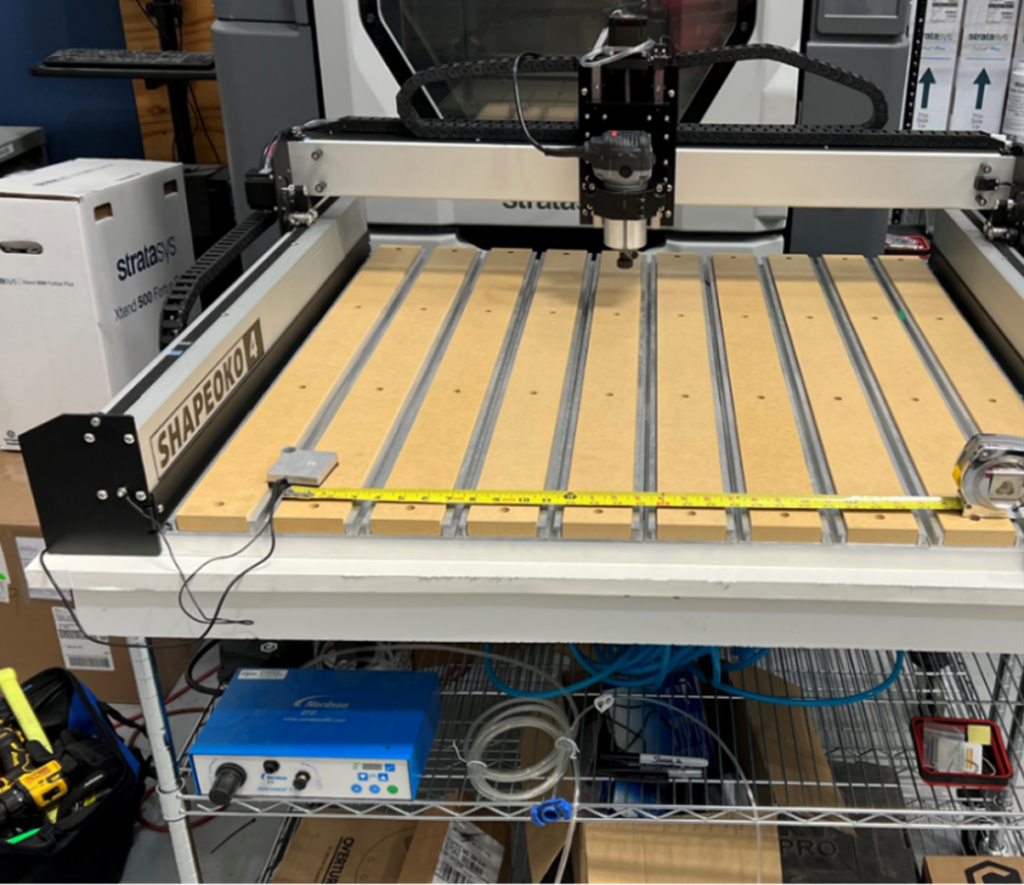
Using the CAD geometry of the parts as a base, the CNC system was programmed in Fusion 360 CAM to 1) travel to the adhesive start point, 2) power on the Nordson dispenser to flow adhesive and 3) travel around the part to lay down the adhesive in the desired profile. By setting this up as a CAM program it was possible to use the CAD geometry as well as the accuracy of the Shapeoko CNC system, below 0.001″, and rapidly iterate and deploy a working program. A simple fixture was made to locate the assembly on the CNC system and ensure the placement of the assembly is repeatable from part to part.
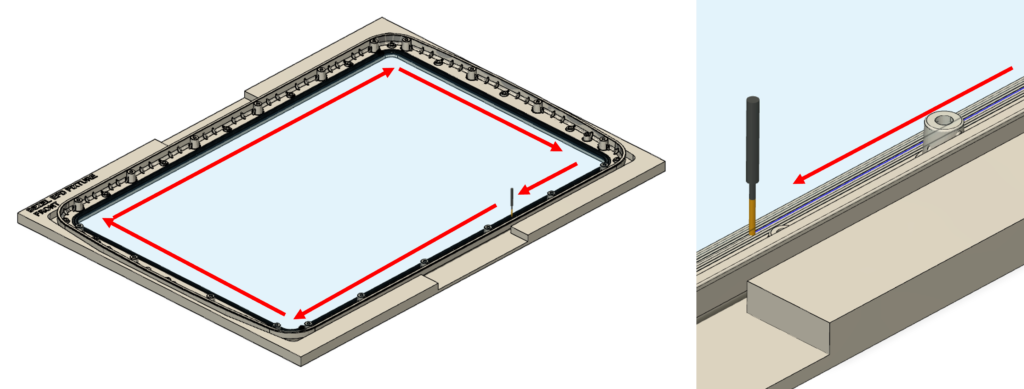
With the CAM program in-hand it was possible to begin trials to dial in the process parameters for the adhesive dispense system. Two parameters set the size of the adhesive bead and the volume of material placed on the assembly; the air pressure output by the Nordson dispense system and the feedrate of the CNC system. These values were dialed in to hit the target adhesive width of 3.5 +/- 0.3 mm and the production time of < 2 minutes, providing for up to 200 units in an 8 hour shift, twice the 100 per day required.
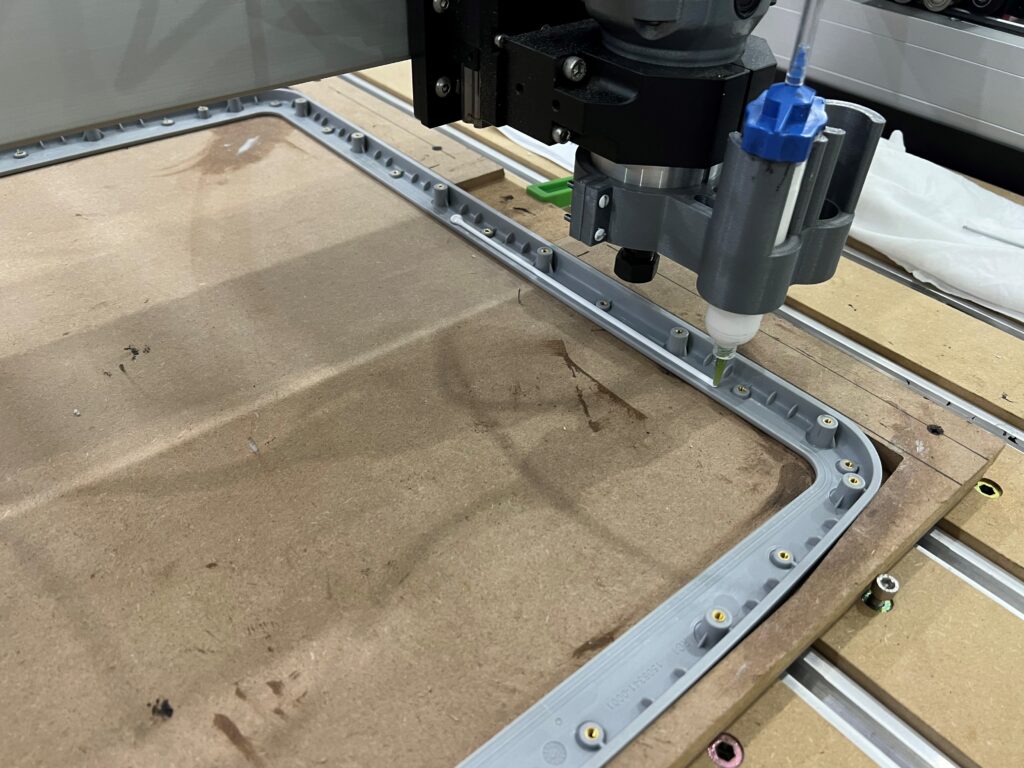
Finally, the dispenser syringe was modified to make the process more user friendly. The original Nordson system relies on a dispenser tube of 30 cc, roughly the size of a large syringe. This required regular refilling of the syringe every 3 assemblies from a 300 cc tube similar to a caulking tube. An air-power caulking dispenser was purchased from McMaster-Carr that would accept the full size 300 cc tube and not require this intermediate fill step. A set of simple parts was designed and built to hold this air-powered dispenser on the CNC system. This system was deployed and the feedrate and air pressure re-tuned to meet the process needs. This modification proved to work very well as a bolt-on replacement for the Nordson syringe.
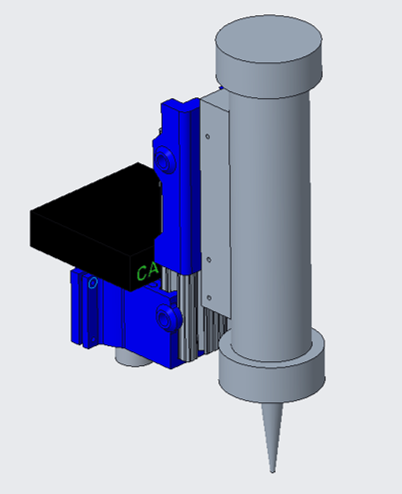
Development work for this system took less than $5000 in components and less than 5 week of part-time effort, well under the cost and lead times quoted by outside vendors. The system served to meet the needs of the project, capable of delivering 2X more units than needed on a per week basis. Work instructions were written and this system was transitioned to production where it has been operating with minimal maintenance producing over 500 assemblies per week.